ASML trekt wat betreft het onderhoud, het refurbishment van complete chipmachines en het as new remanufacturen van onderdelen en modulen graag en veel op met zijn vele suppliers. ‘We realiseren ons dat hightech bedrijven veel van elkaar kunnen leren’, Huib IJkelenstam, head of the re-use & repair program bij de semicon-multinational. ‘En wij hebben natuurlijk een enorm impact op onze supplychain. Dat maakt ons medeverantwoordelijk voor de verduurzaming ervan. Daarom stellen we ons in dit soort gesprekken ook kwetsbaar op. Want juist zo’n houding nodigt gesprekspartners uit open te zijn over problemen die zij zelf ondervinden en nog moeten oplossen.’
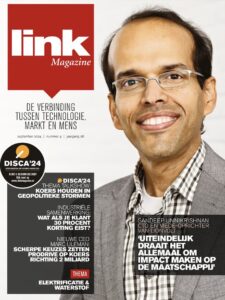
Link magazine september 2024. Thema: Elektrificatie/waterstof.
Vraag exemplaar op: mireille.vanginkel@linkmagazine.nl
Een van die uitdagingen is het nauwkeurig in euro’s kwantificeren wat de waarde is van de – in ASML-speak – reverse flow. ‘We weten wel wat een gebruikt onderdeel waard is, maar alle bijkomende kosten, voor opslag, transport, tooling, handling en – vanwege onze ESG-doelstellingen – CO2-productie, die willen we ook inzichtelijk krijgen, vertelt IJkelenstam tijdens een Captain’s Diner mede georganiseerd door BOOST. ‘Komend jaar willen we naast de repareerkosten ook de bijkomende kosten kunnen koppelen aan het hergebruik van een machineonderdeel. Dit helpt ons bij het verder maken van verantwoordelijke keuzes van wat en hoe we hergebruiken. Dan zou wel eens kunnen blijken dat voor een gebruikt deel bijna net zoveel zou moeten worden betaald als voor een nieuw. Of andersom, dat re-use juist zeer relevant is.’ Eenmaal uitgewerkt wil hij zo’n kwantificeringsmethodiek graag ook laten landen bij toeleveranciers.
Ook de doorlooptijd voor het herstellen van onderdelen, door ASML zelf of – vaker nog – door leveranciers, is nog veel te lang, vanwege capaciteitsproblemen. ‘Daardoor hebben we momenteel voor honderden miljoenen euro aan onderdelen in de remanufacturing en repair backlog zitten’, aldus IJkelenstam. ‘Te lange doorlooptijd dwingt ons nieuwe onderdelen te kopen om productieverstoring te voorkomen. We kijken samen met leveranciers hoe dit te verbeteren, bijvoorbeeld door sporen van gebruik op niet functioneel kritieke gedeeltes van een machineonderdeel toe te staan. Zeker voor kostbare onderdelen interessant.’
Ook capaciteitstekort speelt in dit geval en dus worden er voortdurend extra suppliers gezocht, ook in Azië waar tegenwoordig genoeg kwaliteit zit. Bij voorkeur contractueel via de bestaande toeleverancier, lokaal in de buurt van of bij de klant. Om zo duur – clean verpakt – transport over grote afstand te voorkomen van omvangrijke modules waarin bijvoorbeeld slechts een sensor kapot.