Selo wilde meer controle over zijn processen, om de kosten en levertijden omlaag te brengen en zo de concurrentiepositie verder te versterken. Eind 2019 werd de knoop doorgehakt en gekozen voor de aanschaf en min of meer gelijktijdige implementatie van vier pakketten, waaronder PRO.FILE voor PLM en Ridder IQ voor ERP. Vier jaar later is de digitaliseringslag geslaagd, aldus de hoofdrolspelers. Link Magazine sprak met ze.
– Besloten wordt dat er een grotere ‘onderstroom’ van gestandaardiseerd werk moet komen: minder engineering to order en meer configure to order.
– ‘De eerste stap is te komen tot – wat wij noemen – business understanding.’
– Zo heeft iedereen in het project zicht op wat nog moet worden besteld, op voorraad is of nog binnen moet komen.
– ‘Selo is door de automatisering meer schaalbaar geworden en kan de groei daardoor makkelijker aan.’
– ‘Er is nu veel meer regie.’
Van het ondergaan van ‘tsunami’s’ naar groeibestendig
We schrijven eind jaren tien. Selo Food Group, fabrikant van foodprocessingmachines, wordt steeds vaker geconfronteerd met ‘tsunami’s’ van projecten, waaronder soms heel grote, zoals die van 25 miljoen voor het Duitse Homann. Weliswaar volgen er daarna dikwijls weer periodes van relatieve rust, maar al met al groeit het Hengelose bedrijf in die periode jaarlijks met 15 à 20 procent. En signalen uit de wereldmarkt waarop de onderneming actief is, duiden erop dat de groei van orders zal aanhouden.
Digitaliseringsslag nodig
Het management – ceo Willibrord Woertman en cfo Gerwin Ooms – komt tot de conclusie dat de bedrijfsprocessen efficiënter moeten worden ingericht. Ze betrekken Alfred Klunder erbij, eigenaar van GrowProud, adviseur van maakbedrijven met een groeiambitie, om samen met hem de strategie uit te werken. Besloten wordt dat er een grotere ‘onderstroom’ van gestandaardiseerd werk moet komen: minder engineering to order en meer configure to order, om zo die scherpe pieken van onderhanden werk te spreiden over een langere tijd. Ook moet het vele dubbele invoerwerk, in allerlei Excel-sheets en in een vooral op de handel gericht boekhoudpakket, de geschiedenisboeken in. Net als het feit dat 95 procent van de installed base waar de servicemedewerkers in het veld mee geconfronteerd worden, niet zo op tekening staat.
De conclusie is dat er één digitale backbone moet komen. Dat er een flinke digitaliseringslag nodig is om meer grip te krijgen op de processen, om zo de kosten en levertijden te verlagen en het concurrentievermogen verder te verbeteren. Aldus verhaalt Ooms de business drivers voor de aanschaf en implementatie van vier nieuwe pakketten: ERP, PLM, CAD en P&ID.
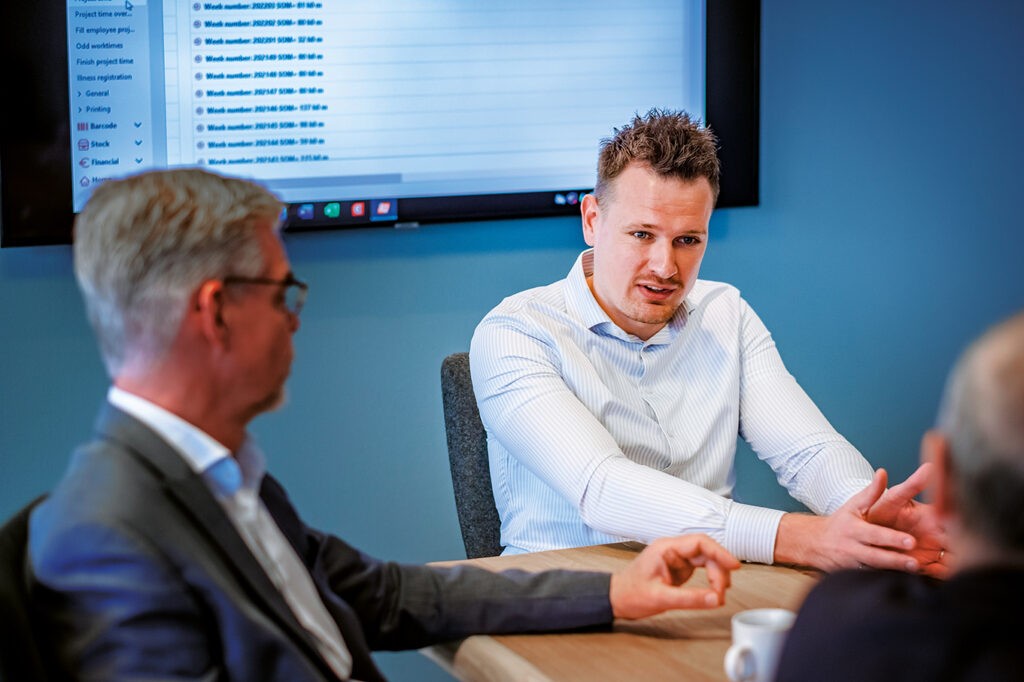
Gekozen werd voor een stapsgewijze implementatie. ‘Om te ondervinden wat er fout kon gaan, en daarvan te leren’, legt Jeroen de Bruijn uit.
Eisen scherp krijgen
Het gesprek op Ooms’ kamer vindt plaats samen met de manager IT & business process engineering van Selo, Jeroen de Bruijn, en met Alfred Klunder. Die laatste krijgt in 2019 de opdracht om samen met de Selo-mensen die digitaliseringslag te realiseren. ‘De eerste stap is te komen tot – wat wij noemen – business understanding. Je moet eerst goed snappen waar de bottlenecks zitten, wat het bedrijf uniek maakt en hoe digitalisering die propositie het best kan ondersteunen’, licht Klunder toe.
Alle data, van sales tot en met service, hebben nu een plek in die ene digitale backbone
Met dat inzicht wordt het pakket van eisen scherp gesteld en kan een begin worden gemaakt met de selectie. Dan wordt contact gelegd met potentiële softwareleveranciers. Die zorgen ervoor dat een delegatie van Selo andere maakbedrijven kan bezoeken. Bedrijven met min of meer hetzelfde procesprofiel als dat van Selo en waar al een digitaliseringslag heeft plaatsgevonden. ‘Op onderdelen hadden die bedrijven het goed voor elkaar, maar niet van A tot Z. Wij wilden het nog beter gaan doen en ik denk dat we nu verder zijn dan die vijf’, duidt Ooms.
Keuzes gemaakt
Eind 2019 worden er knopen doorgehakt. ‘Uiteindelijk hebben we voor het PLM-stuk voor PRO.FILE gekozen en voor het ERP-deel voor Ridder IQ. Behalve dat die pakketten voldeden aan onze eisen, was een belangrijke plus dat PLM Xpert, implementatiepartner van PRO.FILE, en Ridder al meerdere trajecten samen hadden gedaan waarbij beide pakketten waren geïntegreerd’, motiveert Ooms de gemaakte keuze. In december 2019 en januari 2020 zijn de leaseovereenkomsten getekend voor alle vier pakketten, incluis het CAD-pakket SolidWorks en Smap3D voor het ontwerpen van pijp- en leidingwerk. De voorbereidingen voor het live-gaan kunnen beginnen.
Op gang brengen
Dan barst de covid-pandemie los. Even lijkt dat voor de voortgang van de implementaties een blessing in disguise. Ceo Woertman meldt in april 2020 in een persbericht over de voorgenomen digitaliseringsslag: ‘Sommige zaken stagneren, klanten zijn afwachtender en daardoor komt er tijd vrij.’ Maar al gauw blijkt dat covid voor veel ongemakken zorgt, maar niet voor het wegvallen van orders. Integendeel. ‘Omdat veel mensen thuis kwamen te zitten, werden huisdieren veel populairder. De vraag naar petfoodlijnen trok juist nog verder aan’, herinnert Ooms zich. Dus wordt in oktober 2020 Jeroen de Bruijn aangetrokken. Hij heeft de nodige IT-projectervaring opgedaan bij Bronkhorst Hightech en krijgt bij Selo de uitdagende taak de implementatie verder op gang te brengen.

‘De eerste stap is te komen tot – wat wij noemen – business understanding’, aldus Alfred Klunder.
Stapsgewijs
De Bruijn maakt daarbij dankbaar gebruik van het feit dat Selo Food Group uit twee bv’s bestaat. Selo BV die vooral handelt in vleesverwerkende machines; veelal wat minder complexe technologie, goed voor een jaaromzet van 11 miljoen euro. Daarnaast Selo Food Technology BV waar de grote sausproductie- en petfoodverwerkingsinstallaties geëngineerd en geassembleerd worden, een business goed voor 40 miljoen euro. In maart 2021 wordt live gegaan met Ridder IQ en PRO.FILE, alleen binnen Selo BV. Een stapsgewijze implementatie dus, om lessen te kunnen trekken voor die binnen Selo Food Technology, legt de Bruijn uit. ‘Om te ondervinden wat er fout kan gaan, en daarvan te leren.’
Van project- naar voorraadgestuurd
Er moet bijvoorbeeld voorraadgestuurd gewerkt gaan worden, een consequentie van de strategische keuze voor meer cto. Maar die stap zetten, gaat niet vanzelf, heeft De Bruijn ondervonden. ‘Gebruikelijk was dat de projectleiders voor hun project zelf, op order, inkochten en dus veel vrijheid hadden. Maar die artikelen waren niet zichtbaar in de voorraad. Inflexibel, omdat dat uitwisselingen van artikelen tussen project A en B onmogelijk maakte. Anderzijds gaf die manier van werken de projectleiders wel een goed inzicht in de voor hun project opgebouwde kosten.’ Daarom wordt met het Qlik Sense-platform een applicatie gebouwd waarmee de projectleiders met een paar muisklikken de voor- en nacalculatie van hun project kunnen vergelijken. Het draagt eraan bij dat het voorraadgestuurd werken wordt geaccepteerd als de nieuwe standaard.
Long leadtime items
Een ander probleem waar De Bruijn ‘nog wel eens wakker van heeft gelegen’ duidt hij met ‘de long leadtime items’. Door de digitaliseringsslag is het percentage cto-projecten gestegen naar nu zo’n 40 procent. De meeste projecten zijn dus engineering to order. ‘En eto-projecten blijven’, verzekert Ooms. ‘Met eto onderscheiden we ons in de markt. Onze klanten bepalen graag welke motor of welke frequentieregelaar precies moet worden toegepast.’
Het betekent echter wel dat onderdelen met een lange levertijd al moeten worden besteld op een moment dat het ontwerpwerk nog lang niet klaar is, en er dus nog geen bill of material is. ‘Dus is er wat programmeerwerk verricht, zowel in Ridder als PRO.FILE’, vertelt De Bruijn. ‘Nu wordt er in Ridder een stuklijst aangemaakt waarin enkel artikelen met een lange levertijd worden toegekend aan een bepaald project, zodat ze alvast kunnen worden besteld. Maar nog zonder onderliggende engineering- en manufacturing-BOM en tekeningen. Zo heeft iedereen in het project zicht op wat nog moet worden besteld, op voorraad is of nog binnen moet komen en hebben de projectleiders actueel inzicht in de materiaalstatus.’
Alles via Inkoop
Het zijn dit soort lessen die worden meegenomen naar de livegang voor Selo Food Technology in najaar 2021, waardoor dat ‘relatief vlotter’ verloopt. Niet dat het allemaal van een leien dakje gaat. ‘Medewerkers begroeten nieuwe software altijd met enthousiasme, totdat ze er zelf mee aan de slag moeten. Dan wordt er toch voorrang gegeven aan de uitvoering van dat nieuwe project’, benoemt Ooms een vertragende factor.
‘Er was veel vrijheid van handelen en die moest deels worden ingeleverd’, vult De Bruijn aan. ‘Vooral het zelf, direct bij je eigen leverancier, kunnen bestellen was voor projectleiders moeilijk om los te laten.’ Maar inmiddels doet iedereen dat netjes via de afdeling Inkoop. ‘In 2017 hadden we hier één inkoper, nu vijf’, concretiseert Ooms een personele consequentie.
Optimalisatie
Alles draait nu, ook SolidWorks en – binnen Selo Food Technology – Smap3D. Klaar is het nog niet: ‘We zitten nu in de optimalisatiefase’, vertelt De Bruijn. Zo treft Selo momenteel voorbereidingen voor het gebruik van handscanners voor het picken van artikelen uit de voorraad. Maar alle data, van sales tot en met service, hebben nu een plek in die ene digitale backbone. ‘Ik kan nu zien wat de actuele orderintake is, hoeveel offertes uitstaan en wat de kans is dat ze een order worden’, duidt Ooms een paar kpi’s. ‘En onze projectmanagers hebben op elk moment actueel inzicht in hoeveel kosten ze binnen een project tot dan hebben gemaakt. Voorheen moesten ze daarvoor verschillende systemen raadplegen waarin dat werd bijgehouden. Ook al dat dubbele werk is nu verleden tijd.’
Tot slot de hamvraag: heeft de digitaliseringslag inmiddels geleid tot groei? Ooms: ‘Selo is door de automatisering meer schaalbaar geworden en kan de groei daardoor makkelijker aan.’
Implementatie PRO.FILE: ‘We hebben grote stappen gezet’

Design engineer Hessel Diepenveen: ‘Er is meer rust op de werkvloer. Want iedereen kijkt in dezelfde digitale backbone naar dezelfde data.’ Links van hem Hugo Botter.
Selo is helemaal overgegaan op het PLM-platform PRO.FILE. Het vraagt hier en daar nog wel het nodige working around, maar inmiddels werken alle medewerkers in alle bedrijfsprocessen nu met één single source of thruth. En dat zorgt voor meer rust op de werkvloer. ‘Er is nu veel meer regie.’
‘Ik had het vanmorgen nog aan de hand’, vertelt design engineer Hessel Diepenveen. ‘Een van de engineers had gisteren een oplossing bedacht en die in het PLM-systeem gezet. Maar gisteravond schoot hem een net iets betere oplossing te binnen. Dus vroeg hij me of dat nog kon worden aangepast. Maar de order die voortvloeit uit zijn oplossing is automatisch verwerkt in ERP en verzonden naar een leverancier. Dus is aanpassing niet meer mogelijk.’
Dan lijkt de nieuwe, geïmplementeerde IT-oplossing met één digitale backbone voor alle disciplines in het bedrijf misschien inflexibel. ‘Maar voorheen had hij zijn aanpassingen misschien alleen doorgestuurd naar productie, en waren die niet geland bij inkoop, of andersom’, zegt Diepenveen. ‘Waardoor later tijdens de assemblage niet de onderdelen voorhanden waren die op tekening stonden. Vaak leveren kleine technische wijzigingen niet veel voordelen op. Terwijl het voorkomen van situaties waarin het werk moet worden stilgelegd omdat eerst de juiste onderdelen moeten worden nabesteld, wel heel veel tijd en ergernis scheelt.’
Minder ad hoc, meer gestandaardiseerd
Het IT-systeem waar Diepenveen het over heeft, is het geïntegreerde geheel van het PLM-systeem PRO.FILE, het ERP-systeem van Ridder IQ en de Smap3D-pipingoplossing samen met CAD SolidWorks. Behalve Jeroen de Bruijn is ook Diepenveen aangenomen om de implementatiekar te trekken.
Zoals gebruikelijk in migratietrajecten is na een paar jaar veel in orde, maar nog niet alles, zo wordt duidelijk uit het gesprek met Diepenveen en Hugo Botter, directeur van PLM Xpert, de implementatiepartner voor PRO.FILE. ‘We hebben nu alle data in één digitale backbone zitten, maar her en der moeten we er nog handmatig omheen werken, omdat we in de programmatuur nog bepaalde aanpassingen moeten plegen waar we nog niet aan toe zijn gekomen.’
Wissels nog met de hand
Diepenveen, verantwoordelijk voor de standaardisatie en digitalisering van het leidingwerk in de installaties die Selo ontwikkelt en bouwt, kan illustreren waarom nog niet alles voor elkaar is. ‘Idealiter wil je, op basis van de beheerde data in PRO.FILE, met Smap3D je P&ID (piping and instrumentation diagram, red.) maken. Dat is een schematische weergave – en de BOM – van het installatie- en leidingwerk. Om daarmee vervolgens een 3D-pipingmodel samen te stellen. Die manier van werken zou veel tijd moeten schelen. Maar als je er vanuit PRO.FILE mee aan de slag wil gaan, werkt het nog traag.’
‘Dat komt’, licht Botter toe, ‘omdat heel veel data nu steeds weer vanaf de centrale database moeten worden opgehaald. Maar dat is goed op te lossen door het aanpassen van een aantal instellingen in de programmatuur, naar de eigen specifieke wensen. Je kunt zeggen’, stelt hij het metaforisch, ‘dat alle rails van de sporen van alle verschillende IT-systemen er inmiddels ligt, alleen de wissels om van het ene spoor naar het andere te gaan, moeten nu nog met de hand worden bediend. Die bediening gaan we nog automatiseren.’
Meer rust
Begin vorig jaar is Selo helemaal overgegaan op PRO.FILE, maar daarmee is de migratie dus nog niet helemaal voltooid, zoveel is duidelijk. ‘Het is nu eenmaal zo’, legt Diepenveen uit, ‘dat deze migratie moet worden doorgevoerd terwijl het werk aan tal van projecten gewoon doorloopt.’ Evenwel heeft het nu al veel opgeleverd: ‘Er is meer rust op de werkvloer. Want iedereen kijkt in dezelfde digitale backbone naar dezelfde data. Er worden minder fouten gemaakt door het werken met verkeerde versies of onvolledige informatie.’
Voorheen kwam het nogal eens voor dat het wiel opnieuw werd uitgevonden, omdat er onvoldoende inzicht was. ‘Dan werd er een nieuw artikel van een nieuw merk ingekocht. Dat terwijl er al iets vergelijkbaars – van een ander merk – reeds voorhanden was, waarmee de werkvloer vertrouwd was. Dat betekende veel meer variatie en onrust op de werkvloer dan nu. Nu zijn wijzigingen meteen zichtbaar voor iedereen’, aldus Diepenveen. Een aanpassing in het 3D-pipingmodel vertaalt zich in een aanpassing in het 3D-model en dat weer in wijzigingen in de BOM. En vice versa. ‘Er is veel meer regie.’
Grote stappen gezet
Diepenveen is tevreden over de progressie tot dusver: ‘Dat die ene handeling nog niet lekker loopt, is al gauw bepalend voor het oordeel over het geheel. Dat tien andere handelingen vroeger veel meer tijd kostten dan nu, wordt al gauw ervaren als vanzelfsprekend. Zo zit de mens in elkaar. Maar als ik zie met hoeveel gemak en behendigheid onze engineers tools hanteren waarmee ze een jaar geleden nog moeite hadden, weet ik dat we grote stappen hebben gezet.’
GrowProud: holistische aanpak
GrowProud is een advies- en implementatiebureau dat specifiek op de maakindustrie is gericht. ‘Als hecht team van specialisten en ervaren ondernemers staan we voor een holistische aanpak’, vertelt dga Alfred Klunder. ‘Daarmee kunnen diepgewortelde groeibarrières voor maakbedrijven worden geslecht. In onze – bewezen – totaalaanpak worden mensen, strategie en slagvaardige uitvoering onlosmakelijk met elkaar verbonden. Onze specialisten staan daarbij schouder aan schouder met ondernemers.’
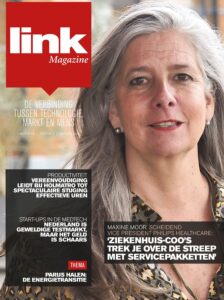
Link magazine april 2023, Thema: Parijs halen: De energietransitie. Vraag een exemplaar op bij de uitgever van Link magazine: uitgever@linkmagazine.nl
Op die manier, wil GrowProud bijdragen aan een florerende maakindustrie in Nederland. ‘Bedrijven vinden in GrowProud een solide gesprekspartner voor het ontwikkelen van groei. Dat kan in de rol van programmamanager en van projectleider, om te zorgen dat het programma van verbeteringen goed wordt verankerd in de dagelijkse praktijk. In de meeste gevallen is interne verbetering de opmaat naar een betere ondersteuning van marketing en sales, wat weer resulteert in een sterke positionering, meer leads en het uitbouwen van export’, zo is Klunders ervaring.
Groeien in de wereldwijde markt van food processing
Op een beeldscherm in de ontvangstruimte van het pand in Hengelo is te lezen waar Selo zich dit jaar zal presenteren. De lijst bevat de grote foodtechnologiebeurzen over de hele wereld, van de VS en Mexico tot Spanje en Thailand. Selo Food Group is een wereldwijde leverancier van voedselverwerkende apparatuur voor de productie van liquid food als sauzen, dressings, soepen en petfood. In Hengelo wordt gewerkt aan zeer lijvige configuraties van ketels, kleppen en pompen, onderling verbonden met pijpen en gedragen door een stevig frame. Die kunnen bedoeld zijn voor de productie van vloeibare margarine, of voor het reinigen van een voedselproductiesysteem van een nog veel grotere omvang. Het bedrijf levert deze oplossingen turnkey wereldwijd, onder meer aan de grootste voedselproducenten ter wereld als Unilever, Nestlé en Mars. De onderneming heeft het hoofdkantoor en een productievestiging in Hengelo, een tweede productievestiging in Oldenzaal, verkoopkantoren in drie andere Europese landen en ongeveer honderd medewerkers op de loonlijst.
In maart vorig jaar zijn de aandelen die het Japanse Omori in het bedrijf had, overgenomen door Rabo Investments. Dat wil – als gevestigde investeerder in het food & agri-ecosysteem – Selo ‘ondersteunen in haar volgende fase van groei’. Een deel van de gelden wordt geïnvesteerd in verdere digitalisering van de bedrijfsprocessen.
MASTERCLASS SMART CUSTOMIZATION/Configure to order op 14 september 2023
Merkt u dat u steeds hetzelfde aan het maken bent, maar dan toch elke keer weer nét even anders? Heeft uw organisatie hierdoor steeds vaker last van verstoringen, kwaliteitsproblemen en uiteenlopende verwachtingen tijdens de orderverwerking? Is het aantal uur engineering per miljoen euro omzet de afgelopen jaren gestegen doordat er per order steeds meer klantspecifieke engineering nodig is?
Als bovenstaande vragen herkenbaar voor u zijn, dan biedt Smart Customization wellicht grote voordelen voor uw ordercreatieproces! Smart Customization is het eenvoudig, efficiënt en foutloos vertalen van de klantwens naar een gestandaardiseerde oplossing.
link Magazine organiseert samen met Post & Dekker, Yellax en Modular5 de masterclass Smart Customization. Daarmee kunt u de kansen en bedreigingen voor uw organisatie traceren, leert u hoe u met Smart Customization een businesscase kunt opbouwen en wat een mogelijke roadmap zou kunnen zijn. Hierbij is hebben van controle over de Bill of Material tijdens het managen van de configuraties hét uitgangspunt!