Drie jaar geleden opende Vergeer Holland zijn nieuwe duurzame kaasverwerkingslocatie. Hypermodern en maximaal geautomatiseerd. Daarvoor betrok het Zuid-Hollandse familiebedrijf zijn partners in een vroeg stadium bij de ontwikkeling. Toeleverancier DERO: ‘Je hebt klanten nodig die je pushen. Dan zie je dat je elkaar in een partnership versterkt.’
Geavanceerde productielijnen Vergeer verwerken ruim 600 ton kaas per week
– ‘Het tijdpad voor groei is van heel veel factoren afhankelijk.’
– ‘De focus heeft continu op de toekomst gelegen.’
– ‘Van elk pakje, zakje of doosje dat de fabriek verlaat, kunnen we exact herleiden van welke kaas dat afkomstig is.’
– ‘Er zit nog veel techniek in die machines die nog helemaal niet bekend is bij onze operators.’
Wie binnenkort over de A12 van Utrecht naar Den Haag rijdt, moet vlak voor de afslag Bodegraven eens naar rechts kijken. Het industrieterrein daar wordt gedomineerd door het 25 meter hoge, zilvergrijze pand van Vergeer Holland. Het gebouw is niet voor niets groots opgezet, want de Zuid-Hollandse kaasverwerker, opgericht in 1934, heeft stevige groeiplannen. Dennis Vergeer, grondstofbeheerder en de derde generatie in het familiebedrijf, vertelt dat er op dit moment meer dan 600 ton kaas per week wordt verwerkt. Samen met de nabijgelegen vestigingen in Reeuwijk en Woerden levert Vergeer Holland in totaal gemiddeld 1,8 miljoen kilo kaas per week aan zijn klanten. En de markt blijft maar groeien.
Vergeer is geen kaasmakerij; het bedrijf koopt kaas in, rijpt het tot de gewenste leeftijd en snijdt het vervolgens in stukken, plakjes en blokjes, of raspt het. Dan gaat het vooral om Nederlandse kaas – niet verwonderlijk onder de rook van kaasstad Gouda. ‘Maar’, haast Vergeer zich te zeggen, ‘we verwerken bijvoorbeeld ook Ierse cheddar, Duitse mozzarella en Deense havarti.’ Zo’n 55 procent van de omzet scoort het bedrijf in het buitenland, de rest van de productie blijft in Nederland en gaat vooral naar supermarkten. ‘We zijn sterk in retailverpakkingen op private label; de huismerken, zeg maar.’
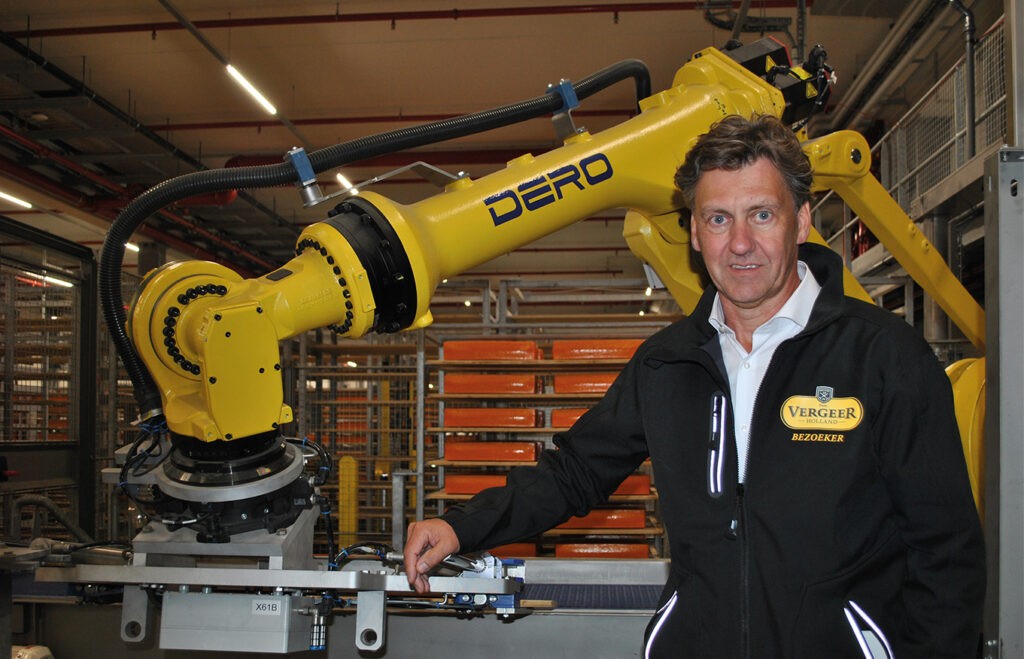
DERO-directeur Maro Dedel: ‘Wat we hier met z’n allen hebben neergezet, is echt het summum van hoe ver je kunt gaan in automatisering.’
Heel veel ruimte
Bij Vergeer Holland werken zo’n vijfhonderd eigen mensen en ongeveer tweehonderd fulltime uitzendkrachten. ‘Om voorbereid te zijn op de toekomst, zetten we sterk in op robotisering en automatisering’, zegt Vergeer. ‘We willen de kazen eigenlijk niet meer met onze handen aanraken. En hier op de nieuwe vestiging in Bodegraven zijn we daarin geslaagd.’
Bij de opzet van de site, die sinds november 2020 operationeel is, heeft Vergeer voortgebouwd op de bijna negentig jaar ervaring in de business. Zoals gezegd, was de grootte van het pand een belangrijke eis. In het verleden was het bedrijf er namelijk al eens tegenaan gelopen dat een nieuwe site alweer te klein was op het moment dat de deuren goed en wel opengingen. Op de smetteloos witte productievloer staan momenteel zes productielijnen, waarbij er nog ruimte is voor twee extra lijnen. ‘En een verdieping hoger hebben we nog zo’n zelfde hal’, vertelt Vergeer. ‘Nu nog casco maar daar kunnen we op termijn nog eens acht productielijnen kwijt.’ Diezelfde uitbreidingsmogelijkheden heeft Vergeer in zijn rijpingsmagazijnen, waar nu plek is voor 4,5 miljoen kilo kaas. ‘Dat kunnen we relatief eenvoudig spiegelen. De ruimte is al beschikbaar.’
Een tijdpad voor de groei wil Vergeer, die samen met directeur – en neef – Diederik Vergeer de familienaam in het bedrijf hooghoudt, niet geven. ‘Dat is van heel veel factoren afhankelijk. Voor een nieuwe klant hebben we onlangs nog twee nieuwe productielijnen neergezet, dus het is nu tijd om even pas op de plaats te maken. Want zo’n uitbreiding heeft impact op de hele organisatie; van inkoop en technische dienst tot aan de uitzendkrachten, iedereen is ermee bezig.’
Summum
De Zuid-Hollandse kaasverwerker heeft de lat voor zichzelf zeer hoog gelegd. Met de site in Bodegraven wilde het bedrijf technologisch klaar zijn voor de toekomst. Daarom betrok het in een vroeg stadium zijn partners en leveranciers bij de ontwikkeling. DERO Groep in Nieuw-Vennep, gespecialiseerd in de automatisering van handlingprocessen in de food en non-food – en met een voorliefde voor kaas – was een van die partijen. Oprichter en directeur Maro Dedel: ‘De focus heeft continu op de toekomst gelegen. Wat kunnen we nu automatiseren? Hoe ver kunnen we gaan? Maar steeds met de groeimogelijkheden in ons achterhoofd. Wat we hier met z’n allen hebben neergezet, is echt het summum.’
Als de kazen binnenkomen, worden ze eerst volautomatisch overgezet naar de interne transportboxen van Vergeer. Op dat moment wordt elke kaas gelijk gepoetst, met vision gecontroleerd, gewogen en digitaal gelabeld. Via een netwerk van shuttles, rollerbanen en liften gaat elke kaas naar de rijpingscel. Daar blijft hij liggen tot hij de gewenste leeftijd heeft bereikt. Voor oude kaas houdt dat een rijpingsperiode tot wel anderhalf jaar in. In die tijd gebeurt er nog van alles, want elke kaas wordt om de drie dagen gekeerd en voorzien van een nieuwe coating.

‘Omdat alles aan het begin wordt geclassificeerd, kunnen we het hele proces optimaliseren’, stelt Patrick Sannes van Viscon (r). Naast hem zijn collega Bart Kunst, commercieel directeur bij Viscon.
‘De grootste winst is dat we met minder mensen toekunnen’
De machines voor dat keer- en coatproces zijn ontwikkeld en geleverd door DERO. ‘Vergeer heeft ons daar echt uitgedaagd en ons meegenomen in hun ambitie om de next level te halen’, vertelt Dedel. ‘Onze standaardmachine had een capaciteit van 650 planken per uur. Dat moesten er 850 per uur worden.’ Het heeft heel wat voeten in de aarde gehad, maar ‘uiteindelijk zijn we daarin geslaagd. We lopen nooit weg voor een uitdaging, maar je hebt ook klanten nodig die je pushen. Dan zie je dat je elkaar in een partnership versterkt.’
Nauwkeurig tracken en tracen
Als de kaas klaar is om te worden verwerkt, wordt hij uit het magazijn gehaald en naar de productievloer getransporteerd. ‘Dat wil je zo slim mogelijk doen, want een kaas die bijvoorbeeld bijna de grens van “oud” heeft bereikt, laat je liever nog even liggen want dan levert hij meer op’, weet Patrick Sannes, business unit director factory intelligence bij Viscon Group. Dat bedrijf uit ‘s-Gravendeel heeft voor Vergeer de volautomatische o en de managementsoftware ontwikkeld. ‘Omdat alles aan het begin wordt geclassificeerd, kunnen we het hele proces optimaliseren.’
Sannes stelt dat het niveau van tracken en tracen in de Vergeer-site ‘heel speciaal’ is. Viscons warehousemanagementsysteem weet van alle producten en materialen precies waar ze zich in het pand bevinden. ‘Van elk pakje, zakje of doosje dat de fabriek verlaat, kunnen we exact herleiden van welke kaas en dus van welke kaasmakerij dat afkomstig is.’
De Viscon-software is de regisseur van het hele productieproces. ‘Als er vanuit het ERP-systeem een opdracht komt, gaat de software aan de slag. Er wordt gekeken welke kazen uit de rijpingscel moeten komen en of ze eerst nog koud of juist warm moeten worden gezet, omdat ze dan makkelijker te snijden zijn.’ Ook gaat er een signaal naar de Kardex-kasten om alle verpakkingsmaterialen, stickers en folies vrij te geven en naar de productielijn te sturen.
Gevoel voor understatement
Zo makkelijk als Sannes nu over de software praat, zo simpel was het allerminst om alles werkend te krijgen. ‘We hadden nog niet eerder zo’n groot en complex systeem gebouwd’, vertelt Sannes. Ook de oplevertijd was een uitdaging. ‘We zouden eerst alleen de besturingssoftware voor het magazijn leveren. Drie maanden voor de livegang vroeg Vergeer ons om ook de aansturing van de productie voor onze rekening te nemen.’ De partij die daarvoor was geselecteerd, liet het namelijk afweten. ‘We hebben dat toen ook op ons genomen; best een uitdaging’, zegt Sannes met gevoel voor understatement. Niet verrassend dus dat de eerste versie van het systeem nog beperkt geautomatiseerd was. ‘Maar de site kon in ieder geval draaien; dat was het voornaamste.’
In het pand in Bodegraven staan niet alleen machines en systemen van DERO en Viscon. Ook onder meer de Duitse machinebouwers Multivac en Weber, het Spaanse Tavil en de Belgische tak van het Nieuw-Zeelandse Scott Automation hebben oplossingen ingebracht. Was het moeilijk om al die systemen met elkaar te laten praten? ‘Het is eigenlijk heel soepel gegaan’, antwoordt Sannes. Uiteraard had Vergeer openheid kunnen afdwingen, maar dat bleek in de praktijk niet nodig. ‘Het zijn allemaal bedrijven die gespecialiseerde machines leveren, en nooit een complete oplossing. Ze zijn het wel gewend om midden in een lijn te staan. Ze kunnen het zich dus niet veroorloven om gesloten te blijven en hun data niet te delen.’
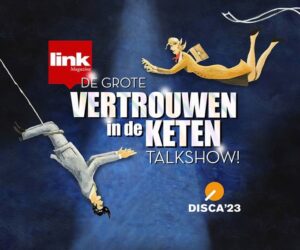
De talkshow gaat vooraf aan de uitreikingen van de drie Dutch Industrial Suppliers and Customer Awards (DISCA). Na de borrel vindt tijdens het diner de live finale plaats van de Dutch Industrial Suppliers and Customer Awards 2023. Programma
Aanmelden disca@linkmagazine.nl
Verbeterkansen
Zoals gezegd, is Vergeer niet van plan op korte termijn weer grote stappen te zetten. ‘De bestaande apparatuur moet eerst volledig in gebruik genomen worden’, zegt Vergeer, ‘want er zit nog veel techniek in die machines die nog helemaal niet bekend is bij onze operators.’
Dedel vult aan: ‘We hebben het over next-level techniek, maar er zijn nog steeds operators nodig om op een knop te drukken of om dingen in te geven. Artificial intelligence is nog niet zo ver dat we helemaal zonder mensen kunnen. Het gat tussen de stand van de techniek en de capaciteiten van de mensen op de vloer wordt wel steeds groter. Wij als leveranciers moeten daar een oplossing voor vinden.’
‘De grootste winst die we hier in Bodegraven hebben geboekt, is dat we met minder mensen toekunnen’, aldus Vergeer. ‘Op termijn willen we deze technologische mogelijkheden ook op onze andere sites gaan inzetten. Dat zal nog een uitdaging worden, omdat we daar vaak met kleinere volumes werken.’ De businesscase ligt dan wat lastiger.
Ook DERO en Viscon zien genoeg verbeterkansen. Sannes: ‘Behalve de uitbreiding naar andere locaties en mogelijke optimalisatievoordelen die dan binnen handbereik komen, wordt het in de toekomst wellicht interessant om nog meer stappen in de site te automatiseren. Dat is uiteraard afhankelijk van hoe de markt zich ontwikkelt.’
En Dedel ten slotte: ‘We willen aan de slag met de installed base. Met onze DGStatistics-tool kunnen we data verzamelen uit het geïnstalleerde machinepark en daar slimme dingen mee doen.’ Sannes vult aan: ‘Er loopt ook een project om met onze software de uitval inzichtelijk te maken, de restanten die na het snijproces overblijven. Wil je daar wat mee kunnen doen, moet je het traceerbaar maken.’