Na tien jaar pionieren met 3D-printen ziet KMWE nu een kentering: 3D-printing is klaar voor industriële toepassing. De voordelen zijn enorm, maar het heeft wel de nodige voeten in de aarde. Om circulair te kunnen werken, sleutelt het Eindhovense bedrijf samen met partners aan een methode om het metaalafval van het reguliere metaalbewerkingsproces om te zetten in poeder of draad waarmee het zijn de 3D-printers kan voeren.
Heuse 3D-printing hub op Brainport Industry Campus
‘De eerste schapen zijn over de dam’, zegt KMWE-ceo Edward Voncken. ‘En dat heeft best even geduurd; we hadden de omslag eerder verwacht.’ Volgens Voncken is de industriële belangstelling voor 3D-printen enerzijds een gevolg van het circulair denken. De ESG-eisen (Environmental, Social & Governance) die aan bedrijven worden gesteld, en de wet- en regelgeving ten aanzien van CO2-uitstootreductie en het hergebruik van materialen, maken dat bedrijven hun producten en processen tegen het licht houden en op zoek moeten naar nieuwe en betere oplossingen.
Anderzijds zijn door de coronacrisis, de supplychaindisrupties, de oorlog in Oekraïne en de handelsoorlog tussen de VS en China steeds meer grondstoffen schaars geworden. De beschikbaarheid van materialen neemt af en de levertijden lopen verder op. Werd 3D-printen tot nu toe vooral toegepast in prototyping en het demonstreren van wat er allemaal mogelijk is, inmiddels is het een oplossing die klaar is om geïndustrialiseerd te worden.

KMWE-directeur Edward Voncken: ‘We zijn al tien jaar met deze ontdekkingstocht bezig en hebben al meer dan 10 miljoen euro geïnvesteerd.’ Foto’s: Patrick Ouwerkerk
3D-printing hub
De hightech industrie vervult daarin een voortrekkersrol. Op de Brainport Industry Campus (BIC) in Eindhoven is inmiddels een heuse 3D-printing hub ontstaan, waar behalve metalen ook kunststoffen en keramiek worden geprint. Om zijn klanten te bedienen heeft KMWE besloten om de 3D-printactiviteiten in een aparte entiteit onder te brengen op de BIC. Die moet in het eerste kwartaal van 2024 operationeel zijn.
‘Een 3D-onderdeel moet nog wel worden bewerkt, gereinigd en chemisch behandeld, maar dat is veel minder werk dan waar een conventioneel onderdeel om vraagt’
Jochem Langendonk, directeur van KMWE’s Global Competence Center, zet de voordelen van 3D-printen op een rij: ‘Ten eerste gebruiken we veel minder materiaal. Op de conventionele manier maken we onderdelen uit een massief blok van een staallegering, aluminium of titanium. Bijna 90 procent van dat materiaal moet worden weggehaald in de vorm van krullen of spaanders. Dat afval moet terug naar de leverancier om tot een nieuw blok te worden omgesmolten. Dat kost tijd en energie. Bij 3D-printen verbruik je minder materiaal, namelijk nog geen 15 procent, en minder energie en is er minder transport nodig.’
Functionaliteit integreren
Een ander voordeel is dat 3D-printen het mogelijk maakt om meer functionaliteit in één onderdeel te integreren en dus meerdere onderdelen samen te voegen. Voncken: ‘Dat maakt de assemblage van het eindproduct eenvoudiger, net als de reparatie van het product en het hergebruik van het onderdeel. We hebben in de lucht- en ruimtevaart een voorbeeld dat er honderd losse onderdelen werden vervangen door een 3D-geprint onderdeel. Bijkomend voordeel is dat het eindproduct lichter is dan het oorspronkelijke ontwerp.’
Ten slotte zijn bij 3D-printen minder bewerkingsstappen nodig vergeleken bij conventionele productie, zegt Voncken. ‘Wanneer je iets weg freest, moeten er bijvoorbeeld pijpjes in gelast worden die vervolgens gesoldeerd moeten worden om te zorgen dat het dicht is. Met 3D-printen maak je alle kanalen in een keer en elimineer je veel bewerkingstappen. Een 3D-onderdeel moet nog wel worden bewerkt, gereinigd en chemisch behandeld, maar dat is veel minder werk dan waar een conventioneel onderdeel om vraagt.’
Andere manier van denken
Om de voordelen van 3D-printen ten volle te benutten, moeten de klanten van KMWE hun product wel opnieuw ontwerpen. Daarbij moeten ze nadenken over hoe ze functionaliteit van verschillende onderdelen kunnen samenvoegen en altijd de circulariteit van het product goed voor ogen houden. ‘Dat vergt een andere manier van denken’, zegt Langendonk. ‘Je moet goed begrijpen wat je met deze technieken kunt en je hele proces van design tot hergebruik onder de loep nemen en aanpassen. Normaal zijn buisjes rond, nu kun je ook een ovaal buisje maken of met karteltjes of bloemetjes. Je kunt het alle figuren geven die nodig zijn. Tot nu toe werd de vorm bepaald door de beperkingen van de conventionele technologieën voor metaalbewerking. Je kunt alleen de hoek om als je er met je gereedschap bij kunt komen, nietwaar?’
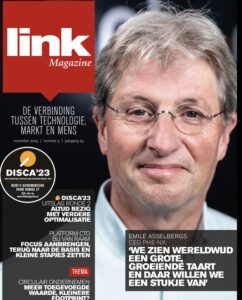
Link magazine oktober/november 2023. Thema circulair ondernemen: meer toegevoegde waard, kleiner footprint? Lees Link magazine digitaal of vraag een exemplaar op bij mireille.vanginkel@linkmagazine.nl
Om klanten te helpen met de omslag in het 3D-ontwerp, geeft KMWE workshops aan engineers en toont de mogelijkheden. ‘Dat is het vliegwiel dat we nodig hebben’, zegt Voncken. ‘Als we laten zien wat een klant heeft bedacht in zijn 3D-ontwerpen, kan dat andere klanten op ideeën brengen voor eigen producten. Dus we doen ons best dat zo veel mogelijk door te geven.’
Het 3D-printproces brengt een verschuiving op gang in de arbeidsintensiteit van het productieproces. Er zullen meer 3D-designers nodig zijn, die nu gelukkig worden opgeleid. ‘Jonge engineers zien 3D-printing als heel uitdagend, om niet te zeggen sexy. Die kunnen straks voor ASML en andere klanten aan de slag. De voorbereiding van een 3D-printproduct vraagt meer aandacht. Maar voor de productie zelf heb je minder resources nodig, de printer staat bijvoorbeeld 74 uur achter elkaar onbemand te printen’, aldus Voncken.
Circulariteit in eigen huis
KMWE ontwikkelde een langetermijnvisie die ertoe moet leiden dat het afvalmateriaal dat in het fabricageproces overblijft, in eigen huis tot nieuwe grondstof voor productie kan worden omgezet. Voncken legt uit dat de gebruikte metalen tot poeder of draad kunnen worden gemaakt waar de 3D-printers mee werken. ‘Zo kunnen we de circulariteit in eigen huis enorm bevorderen. Dat komt de snelheid in het productieproces ten goede, het is goed voor de beschikbaarheid van materialen, we verbruiken minder energie en onze CO2-footprint gaat erdoor omlaag. Dat zijn we nu in samenwerking met partners aan het onderzoeken en ontwikkelen.’
Voor een sluitende businesscase moet KMWE weten hoeveel materiaal het nodig heeft en hoe schoon dat materiaal moet zijn om er poeder van te maken. ‘Samen met de leveranciers van grondstoffen, leveranciers van 3D-printers en onze klanten kijken we hoe we dat kunnen opzetten.’ Zeker is dat er veel meer onderdelen uit de 3D-printers moeten komen, zodat er voldoende behoefte aan poeder is.
‘De grootste investeringen die we nu doen, gaan naar voldoende 3D-printingcapaciteit en naar alle aanpalende processen die we in eigen huis doen, zoals de cleanrooms, reinigingsstraten en bewerkingsstappen. KMWE heeft zo een one-stop-shop gerealiseerd. Daarna gaan we investeren in machines en processen om van metaalafval poeder te maken. We zijn al tien jaar met deze ontdekkingstocht bezig en hebben al meer dan 10 miljoen euro geïnvesteerd in het verzamelen van de kennis, kunde en het machinepark.’ Voncken denkt nog drie tot vijf jaar nodig te hebben om het voor elkaar te krijgen.