Al bijna een eeuw ontwikkelt en produceert Nemag grijpers voor kranen die in zeehavens ertsen, kolen en graan uit scheepsruimen scheppen. Het familiebedrijf is wereldwijd niet de grootste producent, maar wel een zeer innovatieve. Voor de nieuwe generatie grijpers ontving het de prestigieuze IBJ-innovatie-award, een plek in de KvK-top 20 van meest innovatieve mkb-bedrijven in Nederland én een Red Dot voor het design. ‘Wij besparen verladers veel geld.’
Familiebedrijf investeert in productinnovatie en digitalisering proces
Het is deze maandag the day after in de kantine van Nemag in Zierikzee. De flipperkast verlengt de middagpauze voor de vijftig medewerkers met een paar minuutjes; een verhuisbedrijf voert net de bar en de jukebox af. ‘Feestje gehad inderdaad’, zegt general manager Michel Corbeau. ‘We bestaan 95 jaar en dat hebben we in het weekend gevierd met alle medewerkers en gepensioneerde oud-medewerkers mét hun gezinnen. Supergezellig, de kantine was verbouwd tot bruin café met flipperkast. Nemag is nog zo’n echt familiebedrijf met elk jaar wel een jubilaris. Eén medewerker werkt hier al meer dan vijftig jaar. Dat zegt wel iets.’
Wereldwijd gepatenteerd
Feestje of niet, er moet weer gewerkt worden. Want de orderportefeuille zit vol. In de montagehal worden alle zeilen bijgezet om de deadlines te halen. Met man en macht wordt gekant, gelast en gesleuteld aan de enorme stalen grijpers die later hun weg moeten vinden naar zeehavens ergens ter wereld. Meer dan 80 procent van de grijpers wordt geëxporteerd. Naar de Antwerpse haven op een steenworp afstand tot en met die in Noord- en Zuid-Amerika, het Midden-Oosten, Azië en natuurlijk Europa. Aantallen wil Michel Corbeau niet geven en ook de prijs van een grijper is niet publicabel.
‘Snelheid is een belangrijke factor’
Voorlopig ontwikkelt en verkoopt Nemag nog vooral de verschillende traditionele grijpers. Geschikt om droge bulk uit schepen te scheppen. Gemaakt voor zogenoemde brugkranen, lemniscaat-kranen en mobiele havenkranen. Grijpers die nog lang niet uitgefaseerd zijn, maar de toekomst verandert wel. En dus is het tijd voor een nieuwe generatie.
Trots loodst de general manager zijn bezoeker naar de nieuwste grijper: nemaX gedoopt en wereldwijd gepatenteerd. ‘Met deze grijper zijn we dus in de prijzen gevallen. Tien jaar hebben we gestoken in de ontwikkeling, veel geld en mankracht geïnvesteerd. Maar het is het waard.’ De nemaX is uitgebreid getest bij een aantal klanten en potentiële klanten en het oordeel is unaniem: deze is veel beter dan voorgaande generaties. Hij is lichter en kan toch meer bulk scheppen, er kan veel sneller mee gewerkt worden, de kraan vergt minder onderhoud én gaat langer mee. ‘Te mooi om waar te zijn? Ha, dat dachten onze afnemers ook. Daarom hebben we een prototype de hele wereld over gestuurd om onze klanten en geïnteresseerden te overtuigen. Nu komen de orders binnen. Belangrijk, want dit betekent voor Nemag continuïteit op de langere termijn. Precies wat je als familiebedrijf nastreeft.’
Grote druk
Het is de tweede innovatie in vijftig jaar die Nemag op zijn naam schrijft. ‘Dat lijkt niet zo indrukwekkend’, beaamt Michel Corbeau, terwijl hij aan de hand van schaalmodellen uitlegt hoe zo’n kraan met grijper functioneert. ‘In de overslagbranche wordt weinig geïnnoveerd. Iedereen wil bewezen technologie hebben, omdat de afbreukrisico’s hoog zijn. Vijftig jaar geleden hebben we samen met Tata Steel in IJmuiden, toen Hoogovens, een grijper ontwikkeld waarmee efficiënter ijzererts uit de schepen gelost kan worden. Dat is later voor bedrijven met intensieve overslag de standaard geworden.’ Tijd voor wat nieuws dus. Grijpers moesten lichter worden, met meer capaciteit om schepen sneller leeg te halen. ‘Vergis je niet, er staat grote druk op de overslag. Bedrijven moeten tegen steeds lagere tarieven schepen lossen. Duurt het lossen langer dan de vooraf afgesproken tijd, dan moeten ze hoge boetes betalen, zogenoemde demurrage’, verklaart Corbeau. ‘Er meren hier in Rotterdam enorme schepen aan met 400.000 ton ijzererts uit Brazilië, Australië of een ander mijnbouwland. Die schepen hebben een diepgang van 21 meter en kunnen alleen met vloed naar binnen varen. Dan is het zaak om ze in recordtempo te lossen, anders lopen ze bij eb vast. Dat speelt in elke zeehaven, dus snelheid is een belangrijke factor.’
Eerst virtueel bouwen
Lichter en sneller en dus meer capaciteit; dat was de opdracht die Nemag zichzelf stelde. ‘En het scheepsruim moest eenvoudiger worden opgeklaard. De huidige grijpers hebben de neiging om kuilen te graven en komen slecht onder de randen van het ruim. Dat veroorzaakt instortingen van de lading, vertraging en schade. Er blijft veel erts achter dat in het scheepsruim met shovels bij elkaar wordt gereden. Arbeidsintensief, gevaarlijk en kostbaar. Door de vorm aan te passen, zou de grijper overal bij moeten kunnen.’
Een mooi streven, maar niet eenvoudig. In de loop der jaren bracht Nemag al modificaties en verbeteringen aan in het productengamma. Echter, dat was in kleine stapjes en empirisch, die vervolgens bij de klant getest zijn. Omslachtig en niet altijd succesvol. Reden om in zee te gaan met de TU Delft. ‘Met een promovendus van de TU zijn we voor het eerst simulatiesoftware gaan gebruiken. Hierbij is in software ijzererts gemodelleerd waarbij de virtuele ertsdeeltjes zich onderling precies hetzelfde moeten gedragen als bulkmateriaal in de praktijk’, vertelt Corbeau. Eerst zijn testen in het laboratorium gedaan om de juiste instellingen te vinden en uiteindelijk zijn er bij Tata Steel testen gedaan met bestaande grote grijpers in een schip om te kijken of het model klopte. ‘Een intensief proces, zeker in het begin. Elke simulatie van één greep met een virtuele grijper kostte wel één tot twee weken. Toen het model werkte en de simulatie met de werkelijkheid overeenkwam, konden we met onze ideeën aan de slag.’
Productie vernieuwd
In 2017 was het eerste prototype gereed, dit jaar volgt de productie met orders uit binnen- en buitenland. ‘We hebben de afgelopen jaren ook het complete productieproces op de schop genomen’, vervolgt Michel Corbeau. ‘Hiervoor is nieuwe apparatuur aangeschaft, waaronder een 1.000-tons kantpers en een onderpoederlasrobot. Daarnaast hebben we een productconfigurator geïntroduceerd.’ Die stelt Nemag in staat binnen een dagdeel een complete offerte te maken met exacte gegevens over gewicht, capaciteit, de benodigde kraankoppelingen en andere specificaties. ‘Daar hadden we vroeger één tot twee weken voor nodig. Wij maken geen series, elke grijper is klantspecifiek en maatwerk. Uiteraard is het proces in een ERP-systeem gegoten en hebben we volledig grip op inkoop en voortgang in de productiehal.’
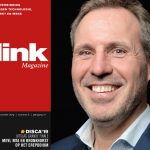
Link magazine december lees de editie digitaal
Oosterschelde
Nemag begon als constructiebedrijf in 1924 in Katendrecht en specialiseerde zich al snel in grijpers. In de jaren zeventig moest het bedrijf plaats maken voor woningen en werd Zierikzee de thuishaven. ‘Hier kon Nemag deze leegstaande fabriek kopen. Een ideale locatie met directe waterverbinding naar de Oosterschelde en toegang tot de havens van Rotterdam en Antwerpen. Meer dan 80 procent van onze grijpers wordt geëxporteerd. De laatste jaren hebben we ook in het pand zelf het nodige geïnvesteerd. Ledverlichting, een luchtzuivering systeem en duurzame koeling.’
Moet de markt nu weer vijftig jaar wachten op de volgende innovatie van Nemag? Michel Corbeau lacht. ‘Nee hoor. Sterker, we hebben weer een promovendus van de TU Delft die bezig is met iets heel moois. Daarvoor doen we ook een beroep op innovatiegelden, waaronder de Europese subsidie OP Zuid. Met onze grijpers wordt overslag efficiënter en goedkoper. Nederlandse innovatie waar we trots op mogen zijn.’
Hoe Nemag een enorme efficiencyslag realiseerde op haar afdeling Engineering
Een geïntegreerde ERP-oplossing
Om de interne processen te stroomlijnen en zich voor te bereiden op de toekomst, moest Nemag een ERP-systeem vinden dat:
- De totale business ondersteunt; van verkoop tot oplevering van eindproduct
- Processen optimaal borgt: minder afhankelijk van mensen en maximaal voorkomen van fouten
- De toegankelijkheid van informatie voor alle afdelingen vergroot
- De Engineeringsafdeling de juiste tools biedt om processen te optimaliseren en tijd te besparen