Het kantoor waarin het interview plaatsvindt, was er nog niet toen GS Metaal anderhalf jaar geleden de aftrap gaf voor de serie in dit blad over de transformatie naar een smart factory. Een open ruimte met veel glas, grenzend aan een zaal waar regelmatig groepen worden ontvangen. Onlangs nog de landenmanagers van Trumpf, belangrijke partner in de transformatie van het bedrijf. En, vertelt directeur en medeaandeelhouder Arnold Hofmeijer, ook concullega’s – die verteld werd hoe het proces verloopt, wat goed is gegaan en ook wat niet.
· ‘Ik denk dat we erin geslaagd zijn de cultuur opener te maken.’
· ‘Eerder op problemen inspringen en ideeën serieus nemen.’
· ‘We werken nu volledig papierloos.’
· ‘Manager moet zorgen voor een sociaal veilige omgeving.’
‘Wij bewijzen dat een bestaand mkb-bedrijf kan digitaliseren’
‘Nee, deze informatie delen met concullega’s kost me geen moeite. Misschien omdat ik zelf niet uit deze sector kom (Hofmeijer was voorheen zakenbankier bij ING, red.). En ik heb niets te verbergen. Waar we nu staan, heeft alles bij elkaar een half jaar langer geduurd dan verwacht, maar we hebben geen productiedag gemist, de doorlooptijd is van vijf naar vier weken gegaan en de leverbetrouwbaarheid is verbeterd, met data aantoonbaar. Wij bewijzen dat ook een bestaand mkb-bedrijf die digitaliseringslag kan maken. Daar ben ik trots op.’
Lean worden
Ten tijde van de eerste publicatie, in april 2018, stond het Vriezenveense metaalbedrijf nog helemaal aan de start van het veranderingsproces. Eerst moest het bedrijf lean gemaakt, dan pas kon er software geïmplementeerd worden. En zo is het gebeurd, verhaalt Hofmeijer. ‘Er zijn duidelijkere afspraken gemaakt die ook worden nagekomen. Zo werkt nu elke afdeling, zowel in de productie als op kantoor, met een dagelijkse ‘dagstart’, een korte meeting van tien, vijftien minuten waarin onder leiding van een van de teamleden besproken wordt wat er die dag gedaan moet worden, of er nog zaken van de vorige dag zijn blijven liggen, of ergens problemen worden verwacht met bijvoorbeeld een machine. Ook is er ruimte om ideeën in te brengen, en die komen er ook. Vaak simpele zaken, van nieuwe bezems aanschaffen tot antivermoeidheidsmatten neerleggen. Maar ook feedback die voor een ander team van belang is. Dan is het aan het management ervoor te zorgen dat er sneller op problemen wordt ingesprongen en dat die ideeën serieus worden genomen. Ik denk dat we erin geslaagd zijn de cultuur opener te maken, dat er meer met elkaar wordt overlegd.’
Software
In de slipstream van het lean-traject is geïnvesteerd in software. Er is een overkoepelend systeem gekomen, de enterprise Service Bus (ESB), die het bestaande ERP-systeem verbindt met het nieuwe MES-systeem van het Duitse XETICS en het CAD-systeem van Trumpf, TruTops Boost. Het concept van die overkoepelende applicatie heeft Attributes, door Jan Bruggink uit Losser bedacht. Het is gebouwd door het Enschede X-IP, samen met mensen van Trumpf en softwarebedrijf Axoom (dat tegenwoordig onderdeel is van het Duitse it-bedrijf GFT, zie kader). ‘We werken nu volledig papierloos, afgezien van de identificatiestickers die we op de producten plakken. Een aanvraag komt als pdf of STEP-file binnen en wordt ingelezen in de calculatiemodule van TruTops Boost. Daarmee rekenen we uit hoeveel bewerkingstijd nodig is en welk materiaalverbruik. En als een leverancier bijvoorbeeld moet poedercoaten, dan voegen we dat nog handmatig toe. Het ERP-systeem zet die informatie om naar een offerte. Wordt het een order, dan wordt de informatie overgezet naar XETICS, dat zorgt dat de juiste digitale tekening op de tablet van de juiste operator terechtkomt. Die kan zich dus niet meer vergissen en hoeft niet meer te zoeken naar de juiste tekening, en hij kan ook direct zien waar het basismateriaal ligt opgeslagen. De kantbankoperator bijvoorbeeld kan op zijn tablet zien op welke stelling het gesneden plaatwerk ligt waar hij mee aan de slag moet.’ Werk dat hij bij GS Metaal meestal doet op een van de kantbanken van Trumpf, maar het gebouwde systeem is ‘open’, zodat hij ook terecht kan op bijvoorbeeld de Safan Darley.
Bouwen, testen, aanpassen
Zodra de order gereed is, wordt dat in XETICS gemeld en na de kwaliteitscontrole wordt vanuit het ERP-systeem de pakbon aangemaakt die naar de transporteur gaat – zodat die met het gerede werk op tijd naar de juiste klant kan rijden, schetst Hofmeijer de laatste (digitale) stappen van het verwerkingsproces zoals dat nu bij GS Metaal wordt uitgevoerd. Een digitalisatie die lastig was, met name omdat het ESB-systeem zorgvuldig moest worden geprogrammeerd om te zorgen dat de data van ERP naar CAD en MES en weer terug steeds goed worden vertaald. ‘Een datum bijvoorbeeld kun je wel op tien manieren schrijven, maar die moet door elk systeem wel steeds herkend worden. Dat gaat niet allemaal in één keer goed; dat is een kwestie van bouwen, testen en aanpassen.’
‘Door de digitalisering gaat nu heel veel in één keer goed, conform de doelstelling’
Dat testen deden de it-specialisten natuurlijk, maar ook de operators op de werkvloer. Soms tegen wil en dank, verhaalt Hofmeijer. ‘Een operator noemde het dan een ‘rotsysteem’. Dan moet je goed doorvragen om te achterhalen waarom hij dat vindt. Het kon zijn dat hij zelfonvoldoende kennis bezat, maar ook dat hij in een gebruikssituatie zat waarmee de it-mensen nog geen rekening hadden gehouden. Die bug moest dan opgelost worden.’
Sociale veiligheid
Hofmeijer raakt daarmee aan ‘het moeilijkste’ van het digitaliseringstraject: mensen erin meenemen. Dat vraagt van hem, als manager, vooral om te zorgen voor een sociaal veilige omgeving. ‘Wij leverden, ook al vóór de digitalisering, nauwelijks fout werk af bij de klant. Maar in ons eigen proces ging er natuurlijk wel geregeld wat mis: misverstanden tussen operators, iemand die een handeling vergeet waardoor zijn collega niet verder kan, een leverancier die verkeerd of te laat levert… Door de digitalisering gaat nu heel veel in één keer goed, conform de doelstelling. En de fouten die nog wel gemaakt worden, zijn nu goed zichtbaar in het systeem. Door er veel over te praten, er veel aandacht aan te geven, kunnen mijn teamleiders en ik ervoor zorgen dat mensen fouten van elkaar accepteren, we voorkomen dat er verwijten over en weer vliegen. Als je gewezen wordt op een fout moet dat ervaren worden als gezonde feedback krijgen, informatie die je helpt het de volgende keer beter te doen.’
Rijkere terugkoppeling
Die feedback kan door het systeem verrijkt worden doordat trends makkelijk ontdekt worden. ‘Ik kan nu makkelijker achterhalen of een bepaalde afwijking vaak voorkomt en wat de oorzaak is. En daar kan ik dan op ingrijpen door die haperende machine te laten servicen of die medewerker extra aandacht te geven.’
De komende maanden krijgt de terugkoppeling uit het systeem verder zijn beslag, niet alleen om afwijkingen te achterhalen, maar ook om machinestoringen eerder te zien aankomen en om nog scherper te kunnen calculeren en plannen. ‘Verdere aanpassing van de software moet zorgen dat we nog beter zicht krijgen op het werkelijke materiaalverbruik en de verwerkingstijden, om zo nog beter te kunnen calculeren. Om scherpere prijzen te kunnen afgeven. Dat is altijd van belang en zeker in de competitievere tijden die er mogelijk aan komen. Ook het planningsysteem gaan we verder verfijnen, volgens de uitgangspunten van quick responsive manufacturing. Dat moet zorgen voor kortere wachttijden en minder onderhanden werk.’
Webportal
Ging het in de eerste fase vooral over digitalisering van de interne processen, in fase twee staat de digitalisering van de communicatie met klanten centraal. Hofmeijer duidt op de online webportal die in voorbereiding is. Daarin kunnen straks orders worden ingevoerd, en de klant kan er snel en 24 uur per dag een prijs opvragen. ‘Het streven is die komend voorjaar in de lucht te hebben.’
Dit is deel 2 van een drieluik waarin de ervaringen van GS Metaal met de opbouw van een smart factory worden opgetekend. Deel 1
‘Al heel wat hoogte gewonnen’
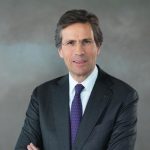
cto Mathias Kammüller
Nu, anderhalf jaar onderweg, is de doorlooptijd verkort en de leverbetrouwbaarheid vergroot. Maar exacte cijfers geven is voor een industriële toeleverancier niet eenvoudig, weet Menko Eisma, managing director van Trumpf Nederland, de belangrijkste partner van GS Metaal bij de ombouw naar een smart factory. ‘Geen week is hetzelfde. Heeft een uitlevering niet plaatsgevonden, dan hoeft dat niet aan de eigen processen te liggen. Wil je de cijfers van vorig jaar goed met die van dit jaar kunnen vergelijken, dan moet je heel goed naar achtergrond kijken. Wij helpen bedrijven als GS Metaal die vertaalslag van cijfers naar conclusies over oorzaken te maken. Onze cockpit laat overzichtelijk de performance zien, en wij ondersteunen het management van de klant in het goed interpreteren van de cijfers. Soms kan een dip in de leverbetrouwbaarheid reden zijn om machines extra onderhoud te geven, een andere keer kan een workshop voor operators beter zijn.’
Dat de opbouw trager is verlopen dan verwacht, heeft vooral te maken met een teveel aan optimisme bij de start, stelt Eisma. ‘Het is net als bij bergbeklimmen: als je na een flinke tijd wandelen omhoog kijkt, lijkt die top nog steeds ver weg. Maar kijk achterom en je ziet dat je al heel wat aan hoogte gewonnen hebt.’
In deel 1 werd aangekondigd dat de overkoepelende softwareschil – Enterprise Service Bus – door Axoom gebouwd zou worden, maar dat heeft X-IP gedaan, met Axoom als partner. ‘Het gaat om maatwerk. Om snel en makkelijk te schakelen, kan dan soms beter zijn met een lokale partij te werken’, verklaart Eisma. Axoom is overigens geen dochteronderneming meer van Trumpf, maar is sinds juli onderdeel van GFT, waarmee Trumpf nauw gaat samenwerken aan verdere standaardisering van software. De reden, aldus cto Mathias Kammüller in een persbericht: dat maakt standaardisering en daarmee de implementatie van smart factory solutions gemakkelijker en goedkoper.